Background
Our client is one of the largest franchisees in the world to one of the leading global beverage manufacturers. They are a key player in the beverage industry that produces and distributes a wide range of carbonated soft drinks as well as non-carbonated beverages and packaged water bottles. It is the second largest bottling company outside the United States of America. The company was incorporated in 1996 and operates 24 hours a day on 4 shifts. They are a major contributor to many sustainability initiatives and are water stewards with key water conservation initiatives set in place including rainwater harvesting, ponds adoption, development & maintenance of wastewater management.
Challenge
Water quality is important not only in terms of safety but also has significant impact on the taste, product integrity, cleaning, and sanitation in the beverage industry. The water that has been contaminated with varieties of pathogenic bacteria can pose a threat not only to human and animal health, but also effects the product down time like the water used in the boilers and cooling towers which must also fulfill high purity criteria with low concentration of concentrated solids passing through these systems. Impure water can accelerate wear and tear, corrosion and scale building, and ultimately reduces efficiency causing costly downtime and increases the repair and maintenance cost. Water can be contaminated in many ways and at any point along the supply chain from the water reservoir to the end user. The contamination happens through physical, chemical, and biological factors during production rendering it unhealthy. So, it’s a challenging task to keep contamination at bay in the beverage industry and hence advanced UV systems are put in place by many global beverage manufacturing companies.
UV is used for disinfection and removal of organic and inorganic contaminants, including chlorine, ozone, and total organic carbon (TOC) and is used largely where conventional chlorine disinfection cannot be applied. This technology helps to improve the taste, color, pH, or odor of water and has better water reusing capabilities meeting sustainability objectives. It is also effective against the cryptosporidium parasite and other water borne pathogens, which is one of the leading causes for acute gastroenteritis.
The beverage company needed to expand their bottled plant line in the Indian state of Telangana. This plant used gallons of water from the nearby lakes and rivers as source water, which had a rare form of Pseudomonas Aeruginosa (PA) bacteria present in it. Identifying and eliminating this baterica from their bottling water process was a critical and challenging task, as the bacteria is very tiny, specific, and rarely spotted in the water. Therefore, the customer needed a UV system which could not only identify this bacteria but also provide a chemical-free disinfection technology at a validated dose and guaranteed performance.
Solution
After much consideration, Evoqua’s ATG™ UV system was selected for their extended plant project. The ATG™ UV SX-225-8 system has a lamp power of 2*2.25 KW with medium pressure (MP) UV lamp technology, which has a 9000-hour lamp life and the highest power density of all the existing UV lamp technology. It can treat up to 5000m3/h with the lowest being 10m3/h, and our client’s current requirement was at a flow rate of 30m3/h in a single, high-output and low footprint UV system. This model has offered our client an increased treatment capacity and flexibility while suiting their sustainability initiatives.
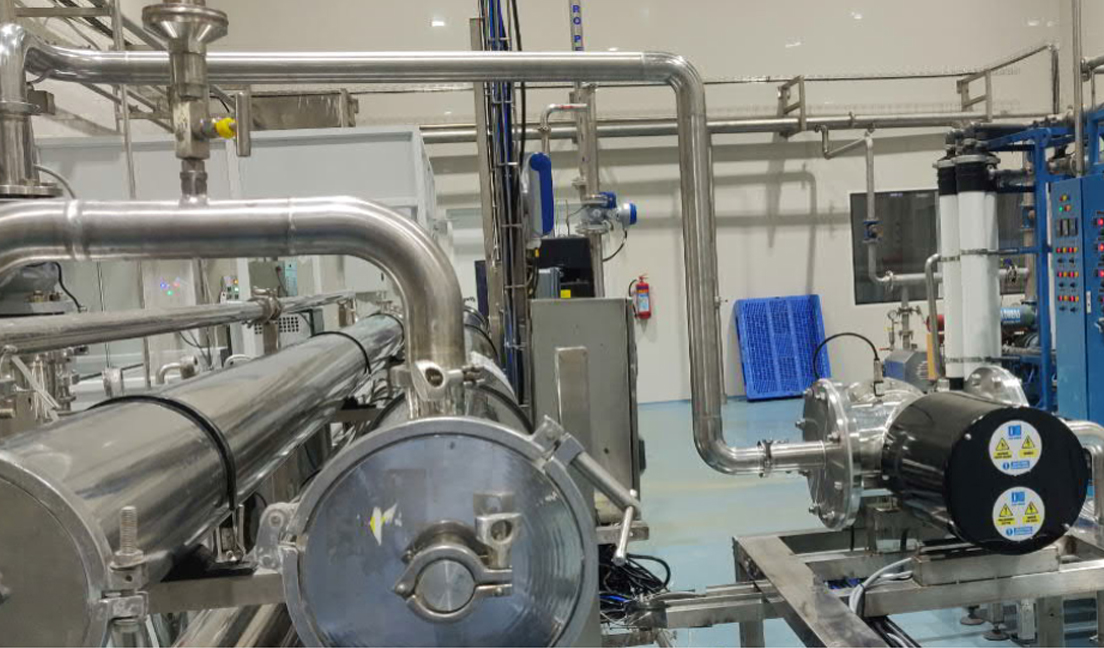
Result
This technology has significantly helped our client avoid product, process, and equipment spoilage which helped control the operational cost and reduce production downtime. It also helped avoid any hazardous process of treating water, maintaining the safety standards, and creating non-toxic by-products. This has enhanced the customers brand image with better by-products in terms of odor, taste, and quality, and maintained the public health in place.
Footnote: Evoqua UV disinfection generator systems undergo third-party validation testing in accordance with the UVDGM (USEPA, 2006). Validated products are tested to confirm a minimum inactivation equivalent of 3 log (99.9%) for microorganisms in accordance with NSF/ANSI 50 and the UVDGM. Performance is not claimed nor implied for any product not yet validated; unvalidated products use single point summation calculations to provide delivered dose recommendations. Performance limitations depend on feed conditions, overall installed system design, and operation and maintenance processes; please refer to Operations Manuals. For more information: contactus@boxmi.cn