Stonyfield is a thriving yogurt business with a modern, sprawling plant in Londonderry, New Hampshire, USA. What began in 1983 as a two-person operation on a small farm has grown over the last three decades to introduce many new products, including yogurt drinks, frozen yogurt, and Greek yogurt.
To handle the increased demand for more yogurt products, Stonyfield upgraded its operation to include sophisticated dairy-processing equipment, allowing the company to expand from selling just quarts of plain yogurt to offering single-serve containers in many flavors. Now, Stonyfield yogurt, made from all natural and certified organic ingredients, is sold in leading supermarkets and natural food stores all across the United States.
Challenge
Stonyfield has always been dedicated to a "healthy planet” and educating its consumers and producers about the value of protecting the environment. Stonyfield’s “Profits for the Planet” program, which supports causes that restore and protect the environment, combined with its “Mission Action Program,” which drives its innovations to have a more sustainable operation, positions Stonyfield as an environmentally responsible model for other businesses.
Plant engineers at Stonyfield work hard to reduce the water and energy used to make yogurt and reduce and recycle waste as much as possible. With this mission in hand, the engineers reviewed a number of different wastewater treatment technologies, vendors, and full-scale treatment systems. They were in the market for a wastewater solution that could bring Stonyfield into the 21st century without compromising their commitment to environmental practices.
Solution
ADI Systems’ wastewater treatment solution best met Stonyfield’s financial, operational, and environmental goals. Stonyfield Farm contracted ADI Systems to design and build a wastewater treatment system to meet newly mandated effluent discharge limits.
This innovative system is designed to pretreat equalized raw process wastewater with chemical oxygen demand (COD), total suspended solids (TSS), and fat, oil, and grease (FOG) levels up to 5,000 mg/l, 550 mg/l, and 500 mg/l, respectively. It consists of two stages: a proprietary Type S low-rate anaerobic ADI-BVF® reactor followed by an ADI® SBR aerobic polishing system. ADI Systems also installed a simple, natural, and robust odor control system to purify the off-gas from the equalization tanks.
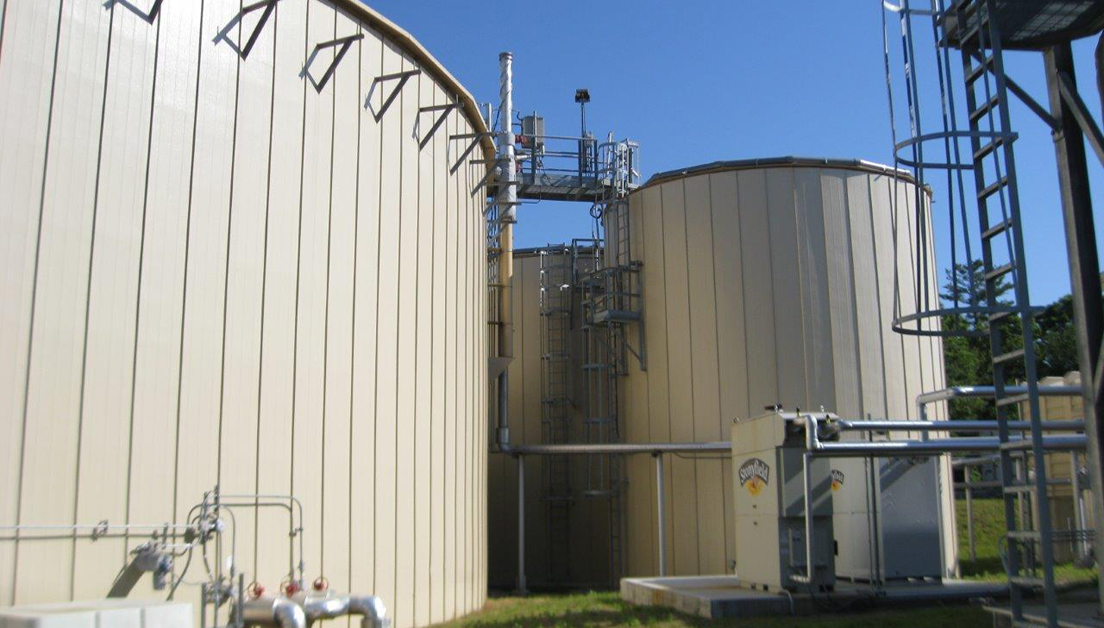
This combination of unit processes readily treats the high-strength, high-solids, high-FOG wastewater found at Stonyfield’s Londonderry plant. The wastewater treatment facility produces minimal waste sludge for disposal as well as a substantial quantity of biogas which is recovered and used to heat the anaerobic reactor, thereby improving anaerobic treatment performance. It also minimizes the overall electrical energy needs for waste treatment.
Results
The wastewater treatment and waste-to-energy system that was created for Stonyfield by ADI Systems allows the company to meet or exceed mandated effluent limits so that it can continue to produce delicious, healthy yogurt products without regulatory penalties. Stonyfield keeps hundreds of organic farmers in business and supports over 100,000 acres in organic production.
The wastewater treatment system incorporates the nurturing, environmentally friendly spirit of Stonyfield’s simple origins into its modernized processing facility. Stonyfield’s commitment to sustainable agriculture practices, which includes ADI Systems’ environmentally responsible wastewater treatment solution, keeps tens of millions of pounds of waste from polluting the planet.
*All trademarks are those of their respective owners.