The Kraft Foods potato chip plant near Kiev, Ukraine (Chipsy Luyks).
Challenge
Due to an expansion in potato chip production, the snack food plant required additional wastewater treatment capacity. It needed to be able to meet strict discharge limits for biochemical oxygen demand (BOD), total suspended solids (TSS), ammonia nitrogen (NH3-N), total nitrogen (TN), and total phosphorus (TP) regulations.
Solution
ADI Systems was selected to upgrade the existing treatment plant, which included a proprietary low-rate anaerobic ADI-BVF® reactor. ADI Systems ultimately provided an ADI® membrane bioreactor (MBR) technology package that would meet the need for additional capacity while discharging high-quality effluent to the local watershed.
The upgraded treatment system continues to use the BVF® reactor, which anaerobically pretreats the raw wastewater. The anaerobic effluent then flows to an MBR, which is designed to offer final treated effluent that is low in nutrients, BOD, and TSS concentrations.
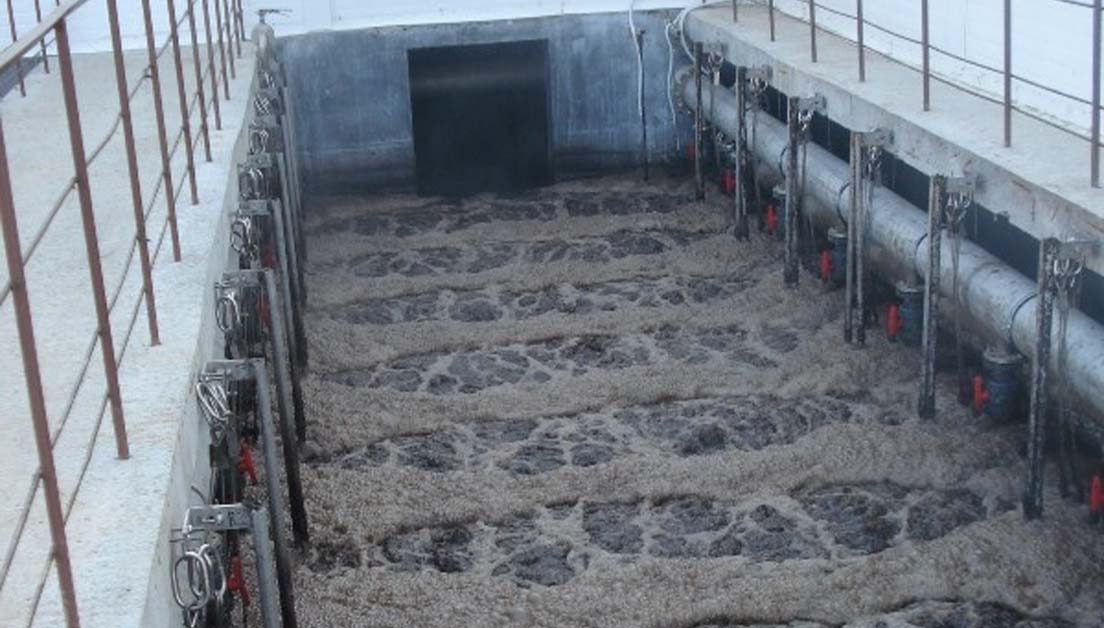
Results
The MBR was selected due to its resiliency and dependability to meet the required effluent limits. The MBR system is designed to treat a total flow rate of 2,200 m3/d (581,000 gpd) (anaerobic effluent and primary clarified wastewater [carbon bypass]).
The MBR produces effluent with BOD and TSS concentrations of <6 and <4 mg/l, respectively. It meets all nutrient discharge limits, with effluent concentrations of NH3-N and TP of <2 and <1 mg/l, respectively.
The MBR is operated to provide simultaneous nitrification and denitrification, which allows the potato chip plant to achieve excellent nutrient removal. Each membrane tank includes 10 submerged membrane units.
The Kraft Foods’ MBR plant now consistently produces a high-quality effluent suitable for direct discharge.