Challenge
Self-cleaning screen filtration systems are, experienced plant managers say, a familiar technology. After all, hundreds of them are installed worldwide every year. They are most appropriately used in "high flow, low load" environments and therefore, not usually associated with being effective when filtering organic material, especially from rivers where the water quality can change on a daily basis. However, the need to conserve water, space considerations, and other factors are moving municipalities and industrial companies to look anew at this increasingly vital technology.
New Brunswick-based Irving Tissue paper mill had been using an older carbon steel filtration technology to process raw intake water from a nearby river into its plant. Faced with an obsolescence of existing parts combined with the advantages of newer filtration technologies, Irving Tissue decided it was time to replace the outdated 18-year-old system.
Solution
Evoqua's VAF V-1500 stainless steel self-cleaning filters with custom 316 stainless steel mainfold provided the ideal solution.
We teamed up with our Canadian distributor to supply not only a state-of-the art filtration package, but also a custom programmable logic controller (PLC) package that interfaced with the Irving Tissue maintenance control system. Onsite training and service support to the plant were also provided.
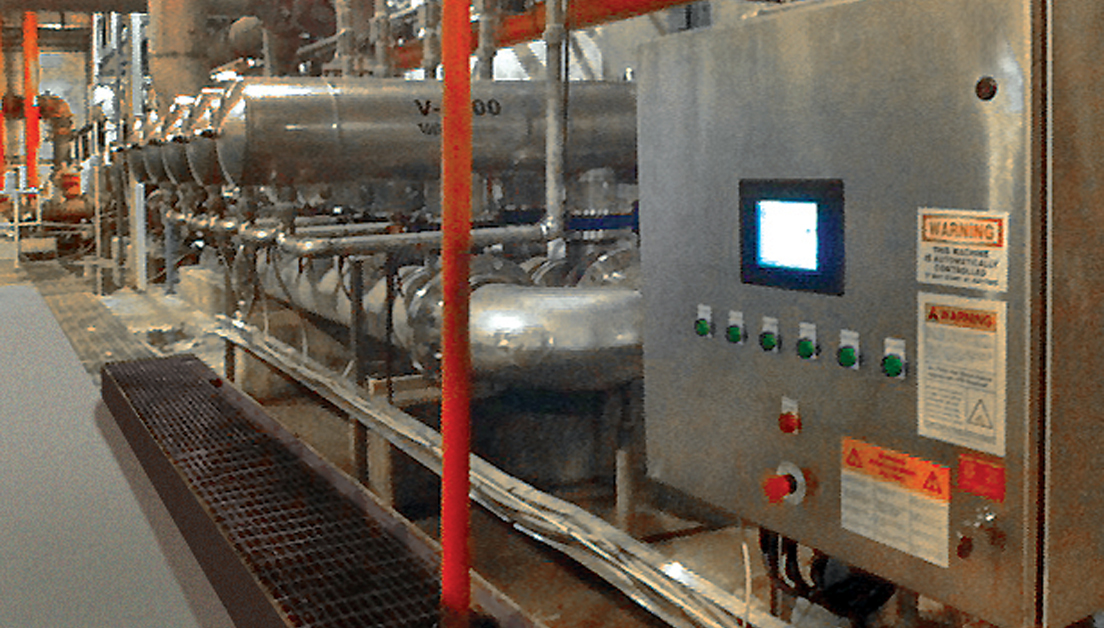
Results
Delivered and installed in 10 weeks, the new system has a small footprint and reduces the flushing volume to less than 1% of the total flow. The frequency in which the flushing cycle initiates also decreased from 15 minute intervals to 40 minutes in between cycles. At the same time, the amount of intake water filtered increased from 159 m3/hr to 454 m3/hr (700 to 2,000 gallons per minute).
The patented* mechanical barrier screen filters utilize a self-cleaning technology that does not require external motors, pistons, limit switches or gearboxes to reverse the cleaning mechanism. There are no external seals eliminating any potential leak points. There are fewer moving parts which results in an inherently simpler system requiring less maintenance and reducing overall operating costs. Additionally, in just one pass of the cleaning cycle, the entire screen surface is cleaned. The cleaning process takes only 15 seconds, and the screen is traversed at least four times.
*Patented in some countries
" We chose the VAF system for several reasons; it was the most cost effective solution with the least amount of moving parts. It’s a first rate system and looks great. "